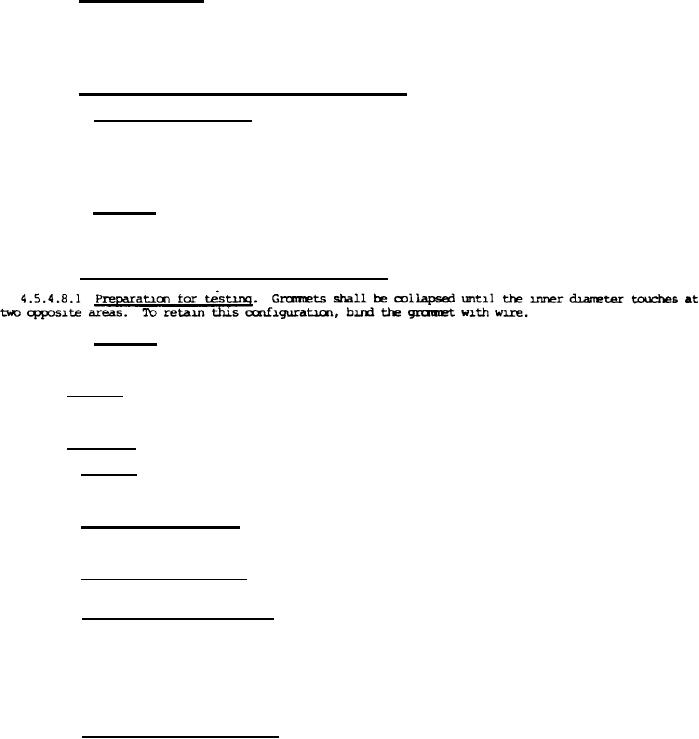
ZZ-V-25E
4.5.4.6 Air flow rate test. To determine conformance to 3.6.1, for 30 seconds valve assembly shall be
subjected to clean and dry air flow delivered by a standard air duck through a 1/4" inside diameter
air hose 25 feet long. Pressure at the inlet end of the hose shall remain between 90 and 100 psig for
duration of the test. The receiving tank, on which the valve assembly is mounted shall have a capacity
of 1.3 to 2.5 cubic feat, and shall be precharged to 5 psig before beginning the test. For calcu-
lations, tills test shall be considered to & performed under isothermal conditions.
4.5.4.7 Valve stem ozone resistance test, when specified
4,5.4 .7.1 Preparation for testing. Valve stems, at least 72 hours old, shall be lubricated with soap
solution and mounted in the base plate (figure 1). Valve stems skill then be washed with cold tap water
for at least 15 minutes to remove the lubricant. Valve stems shall be bent 10° away from normal
perpendicular position (80° with relation to the base plate). Care shall be taken that valve stem pairs
retain the prescribed angular position for the duration of the test. The valve stem-and-plate com-
bination shall be placed in an ozone chamber.
4.5.4 .7.2 Procedure. To determine conformance to 3.5.1, valve stems Shall show no evidence of
Cracking when being ispected under 5-power magnification, after being subjected to an ozone concentration
of 50 + 5 parts of ozone to 100,000,000 parts of air, by volume, for 40 hours, at a temperature of 100° ±
5°F.
4.5.4.8 Grommet ozone resistance test, when specified.
4.5.4 .8.2 Procedure. To determine conformance to 3.2.5.1, grommets shall show no evidence of cracking
when inspected under 5-power magnificaiton, after being subjected to an ozone concentration of 50 ± 5
parts of ozone to 1000,000,000 arts of air, by volume, for 72 hours, at a temperature of 100° ± 5°F
4.5.5 cap test. To determine conformance to 3.6.2, cap shall demostrate no leakage while
finger-tight on valve stem having no core, under s[pecified pressure, the valve being immersed for the
specified time.
4.5.6 Core tests.
4.5.6.1 Fit test. To determine conformance to 3.3.3.1, valve core threads shall demonstrate no
visible damage or engagement roughness during or after 16 cycles of being tightened into a previously
unused valve stem and subsequently loosened.
4.5.6.2 Pressure retention test. To determine conformance to 3.6.3.2, valve cores shall be installed
in test manifold, and while immersed for leakage observation, be subjected to the specified internal
pressures for the specified length of time.
4.5.6.3 Air flew input rate test. To determine conformance to 3.6.3.1, valve cores shall be subjected
to the same air flow rate test as that specified herein for valves (see 4.5. 4.6).
4.5.6.4 Low temperature leakage test. Previously unused and untested cores shall be installed in a
test manifold at specified pressure in manifold and the entire assembly shall be lowered to the specified
temperature. After 24 hours of conditioning at the specified temperature and pressure, cores shall be
checked for 1 minutes at specified temperature and pressure for leakage. After leakage test, cores and
assembly shall now be allowed to rise to ambient temperature the specified pressure being maintained, and
the cores again checked for 1 minute for leakage, To conform to 3.5.1.1, no excess leakage shall be
registered during any of the leakage tests mentioned in this paragraph. However, retightening is permitted
if leakage is found.
4.5.6.5 High temperature leakage test. Previously unused al-d untested cores shall be installed in new
tank stems and the tank stems Installed in the test manifold The complete assembly shall be placed in an
over and conditioned for 24 hours at specified temperatures and pressure. Then the cores shall be checked
for 1 minute for leakage, in water at the specified temperature, except that no water shll be above
200" F. At this point , should any Of the cores be leaking, half of those leaking shall be retightened to
determine whether the cup gasket or barrel gasket caused the leakage and the leakage status of all cores
recorded. The assembly shall now be allowed to cool to ambient temperature the pressure being
maintained . The cores shall again be checked for 5 minutes for leakage. If leakage is discovered.
retightening is again permitted. To conform to 3.5.1.2, no excess leakage shall be registered during any
of the leakage tests mentioned in this paragraph. Non-retightened cores shall be removed, the removal
torque being recorded as well as the condition of each barrel gasket.
10
For Parts Inquires call Parts Hangar, Inc (727) 493-0744
© Copyright 2015 Integrated Publishing, Inc.
A Service Disabled Veteran Owned Small Business